Interphex
Automation NTH Showcases Vision Guided Robotic Wire Insertion Machine
Engineered to address the tight-tolerance assembly of two common medical device sub-components: stylets and cannulas.

Automation NTH, an automation system integrator specializing in complex life sciences, medical device and med tech manufacturing challenges, is showcasing a precision automation solution for complex medical device assembly at INTERPHEX. The company is providing live demonstrations of its custom-designed Vision Guided Robotic Wire Insertion Machine, a precision solution that can control movement with less than 0.001” (25 µm) tolerance in all axes. The machine was engineered to address the tight-tolerance assembly of two common medical device sub-components: stylets and cannulas.
Stylets are flexible metal wires often as miniscule as 0.010” (0.254mm) in diameter. Cannulas are hollow, exceedingly narrow tubes with inner diameters of approximately 0.013” (0.3302mm). Cannulas are frequently used to house needles or stylets for IVs and syringes.
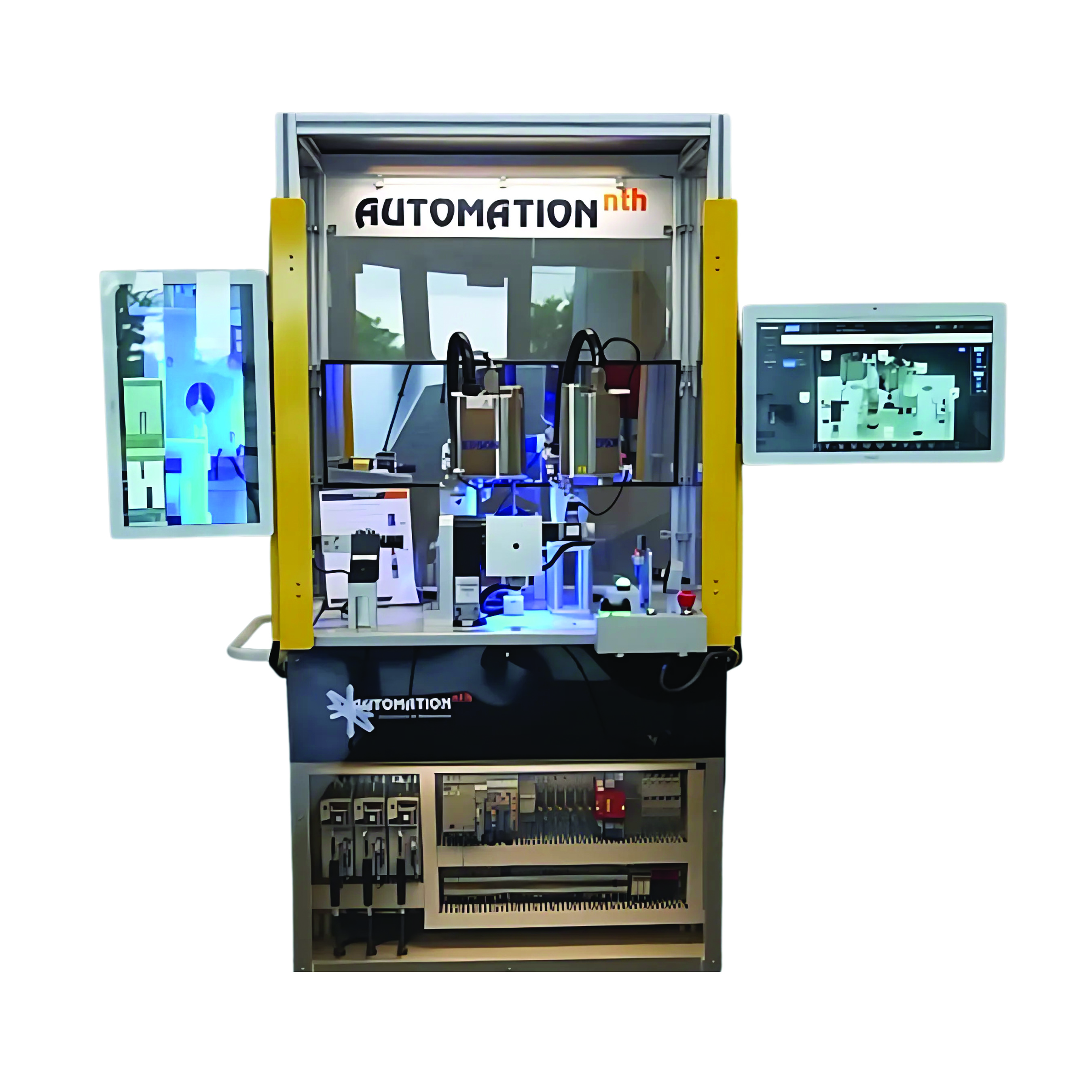
The wire insertion process requires accuracy of ± 21 µm, angular tolerance of 1.5°, and robot movements with ± 5 µm accuracy. From a quality control standpoint, stylets must not touch the inner wall of the cannula, which could damage the stylet. Variability is also a concern, as stylets differ in key attributes such as wire bends, angles, and lengths. Considering this, any machine solution must be exceptionally flexible.
Automation NTH addresses these challenges by utilizing a Selective Compliance Assembly Robot Arm 4 (SCARA 4) axis robot, along with two tabletop-mounted servo motors permitting independent motion. The configuration allows the machine to tilt the syringe, holding the cannula in the Theta X and Theta Y directions to handle angle variability in the stylets. To accommodate for stylet variability, the machine utilizes vision to guide the robot into position, then aligns the cannula with the stylet for insertion.
Automation NTH’s Vision Guided Robotic Wire Insertion machine incorporates a robotic gripper, which picks a cannula from a nest and threads it into the syringe body, fixing it into place. A corresponding robotic arm then picks a stylet from the nest and moves it to an approach position, presenting it to inspection cameras that record and measure offsets.
The system employs a delicate feedback loop between the robot, camera, and servo motors. The cameras record and measure, while the robots adjust the stylets and cannulas as needed based on this information. The process is then repeated until the stylet is lined up within ± 21 µm, achieving this incredibly tight tolerance via a “progress until perfection” setup.